Creating a Model for a Sealed Mechanical Design System
Introduction Mechanical seals play a crucial role in maintaining the efficiency and reliability of high-load rotary machines. The complexities involved in their design, particularly the interaction between frictional, thermal, and hydrodynamic processes, necessitate advanced modeling to ensure optimal performance. This blog post delves into the development of a closed design model for mechanical seals, examining the challenges, methodologies, and results.
Understanding the Challenges in Mechanical Seal Design Designing mechanical seals involves addressing issues such as uneven wear due to angular deformations, thermal and mechanical load impacts, and potential leakage. The model must accurately predict parameters like friction power consumption, seal durability, and hydrodynamic characteristics of the sealing gap. The simultaneous influence of friction, hydrodynamics, and temperature makes the process particularly complex.
Modeling Methodology A robust design model needs to incorporate both the sealing and bearing capacity mechanisms. In the model discussed by Shevchenko, a confusor or diffuser gap shape is considered to ensure the hydrodynamic support needed for stable, non-contact operation. The development of this model focuses on:
- Analyzing the behavior of the sealing surfaces under different operating conditions.
- Predicting the interactions between the rotating and stationary rings of the seal.
- Ensuring a transition from initial dry friction to a fully developed liquid friction regime.
Key Findings and Insights
- Hydrodynamic Support: The model demonstrates that hydrodynamic support is critical for maintaining a non-contact operation. A decrease in film thickness during rotation increases this support, contributing to a stable seal operation.
- Impact of Thermal Deformations: The influence of temperature changes across the sealing surfaces was found to cause axisymmetric deformations that impact the sealing performance. Effective heat management and deformation analysis are thus essential.
- Lubrication Dynamics: The transition from boundary to liquid friction is influenced by the flow of lubricant in the sealing gap. This is largely determined by the gap’s geometry and the sliding speed of the sealing surfaces.
Design Considerations For effective mechanical seal design, it is necessary to:
- Incorporate a mathematical description of the processes within the sealing gap.
- Optimize the gap shape to maximize the rigidity of the lubricant film.
- Consider external factors like the elastic properties of secondary sealing elements and load variations to maintain non-contact sealing.
Conclusion The development of a closed design model for mechanical seals provides valuable insights into achieving reliable, long-lasting performance in high-load applications. By addressing the key challenges of uneven wear, thermal impact, and lubrication dynamics, engineers can create more effective seal systems that ensure stability and efficiency.
Tags: Mechanical Seals, Engineering Design, Hydrodynamic Lubrication, Thermal Deformation, Seal Reliability, Engineering Models
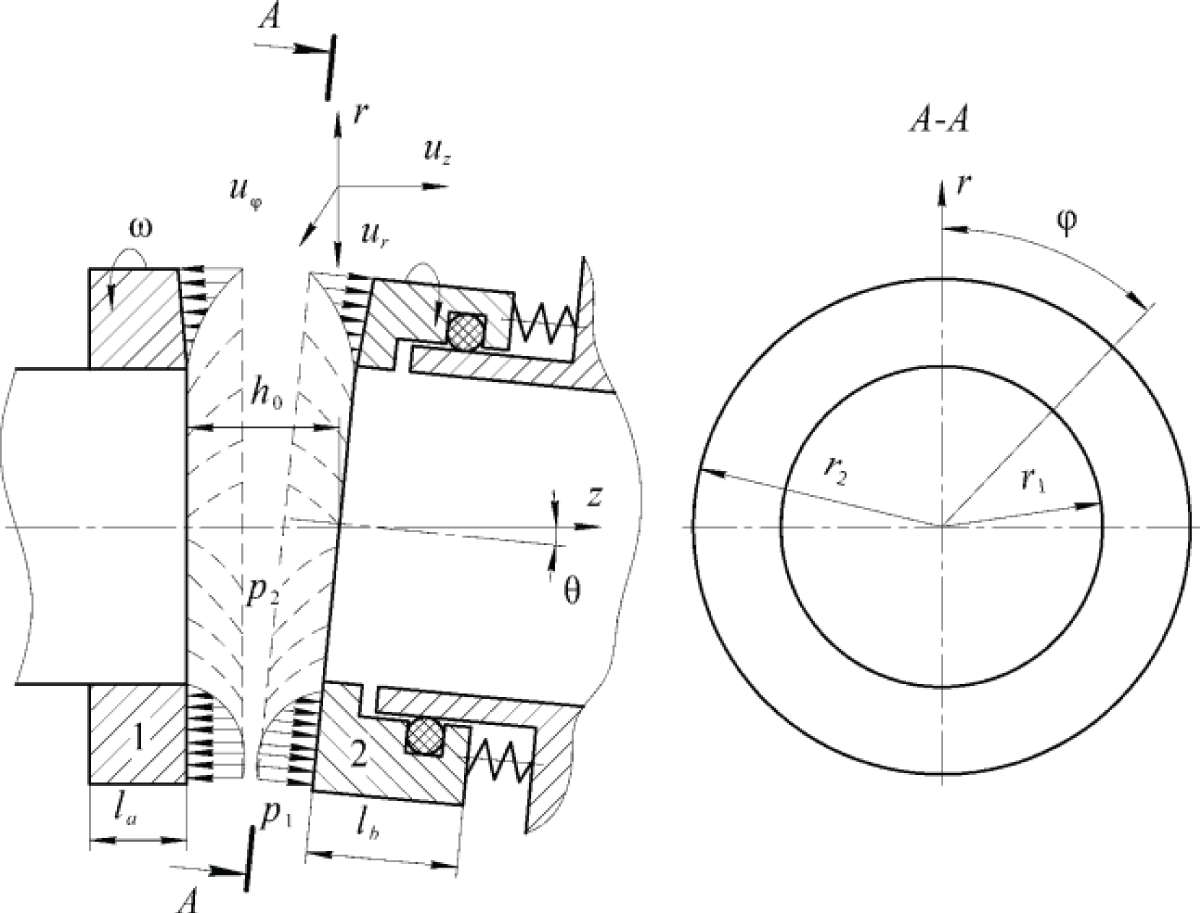
Scheme of the end gap of the sealing unit after it enters the liquid friction mode with the determining influence of hydrostatic forces. Let’s introduce the following definitions: r, z, are radial, axial, and angular coordinates; u,r, u,z, u,φ are the radial, axial, and angular velocities of the medium flow; ω is the angular velocity of rotation of the ring; p1, p2 - pressure before and after the seal; Fn is the force of the elastic spring element; h0 - the average gap between the sealing surfaces; la, lb are the body heights of ring A and ring B, respectively; θ - the angle of non-parallelism of the sealing surfaces of the rings; r1, r2 - inner and outer radii of the sealing surfaces of the rings.