Analysis of Damage to BKZ-160-100-GM Boiler Screen Tubes (Barnaul Boiler Plant) After Upgrading Steam Production Capacity from 160 t/h to 210 t/h (Fuel: Natural Gas/Fuel Oil, Pressure: 100 kgf/cm²)
Introduction
In the quest for higher efficiency and productivity, boilers undergo significant modifications. One notable example is the reconstruction of the BKZ-160-100-GM boilers at the Barnaul Boiler Plant. Designed for steam productivity of 160 t/h at a pressure of 100 kgf/cm², these boilers were upgraded to achieve a productivity of 210 t/h. While the reconstruction led to enhanced performance, it also revealed challenges, including widespread damage to the boiler’s screen tubes. This post explores the causes and implications of these damages, based on the findings of Popov et al. (2024).
Boiler Reconstruction Overview
The reconstruction involved:
Conversion from pulverized coal combustion to natural gas/fuel oil.
Implementation of a two-stage evaporation scheme for improved steam quality.
Replacement of the phosphate treatment with a chelant-based regimen using Trilon B.
Modifications to the chemical water treatment system to enhance feedwater quality (e.g., reducing hardness and silica levels).
These changes aimed to boost steam productivity and operational efficiency, ensuring the boilers met modern industrial demands.
Causes of Screen Tube Damage
Despite the benefits, damages to the screen tubes became evident shortly after reconstruction. Key findings include:
Corrosion and Deposits:
Internal deposits consisting mainly of iron oxides formed on the fire-exposed side of the tubes.
These deposits created localized overheating and steam layer formation, leading to metal corrosion and ruptures.
Circulation Issues:
Water circulation in the side screens remained stable, eliminating it as a primary cause.
Higher salt concentrations in the water supplied to certain tubes intensified corrosion.
Thermophysical Properties:
Changes in deposit structures during the transition to chelant-based treatment caused delamination, increasing susceptibility to overheating and corrosion.
Impact on Boiler Performance
The damages included multiple leaks and metal ruptures, significantly affecting boiler reliability. Key observations include:
Localized Damage: Only 14 tubes on the side screens were affected, primarily those in angular panels.
Reduced Operational Integrity: Boiler shutdowns occurred due to feedwater and steam imbalances caused by ruptures.
Solutions and Recommendations
To address these challenges, the following measures were implemented:
Replacement of damaged screen tubes.
Enhancements to chemical water treatment protocols to prevent aggressive water impact.
Routine inspections and monitoring to detect and address corrosion early.
Conclusion
The case of the BKZ-160-100-GM boilers underscores the complexities involved in boiler reconstructions. While modernization efforts significantly improve performance, they also necessitate careful consideration of material durability and chemical processes. By addressing the root causes of screen tube damages, the power plant successfully restored boiler integrity and ensured long-term operational reliability.
Tags: boiler reconstruction, screen tube damage, BKZ-160-100-GM, natural gas boilers, corrosion, steam productivity, energy engineering

Main parameters of the boiler and circulation velocities with changes in boiler load Boiler drum pressure.
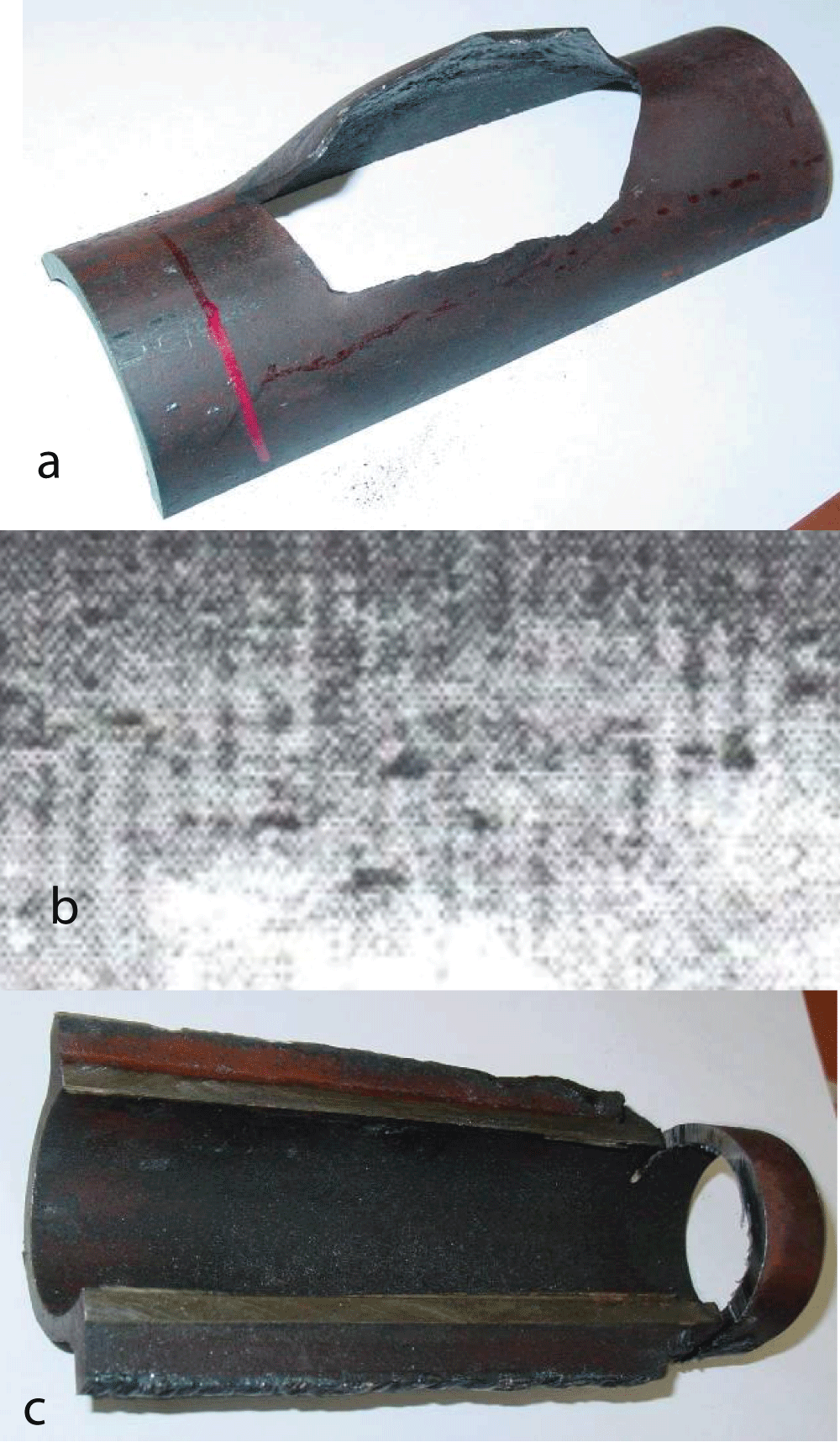
Photograph of a damaged tube. Here, a) Fire half of the tube; b) Internal surface of the fire half of the tube; c) Internal surface of the back half of the tube.